3D-printed RC kit for 1/87 vehicles
The goal of this project is to make an RC conversion kit (mostly drivetrain and a steering system) for 1/87 trucks. Usually these parts are made of metal, especially gears, worms etc. The idea is to try and replace metal with hobbyist-grade 3D-printed parts as much as possible. Currently the verdict is that this can be achieved and resin-printed parts are sturdy enough for this purpose, even from standard resins.
Files for 3D printing are available here:
Demo: RC conversion of Volvo FH16
As an reference implementation of the RC kit, I am converting a Volvo FH16 from Herpa to RC.
The truck has following features:
-
driving motor
-
steering servo
-
lights (14 in total)
-
2 head lights
-
4 blinkers, 2 in front, 2 in the rear
-
2 brake rear lights
-
2 reverse lights
-
4 sideskirt lights
-
(maybe) a connector for trailer functions.
Creating the model of truck frame was relatively easy, except it took several iterations to get dimensions right.
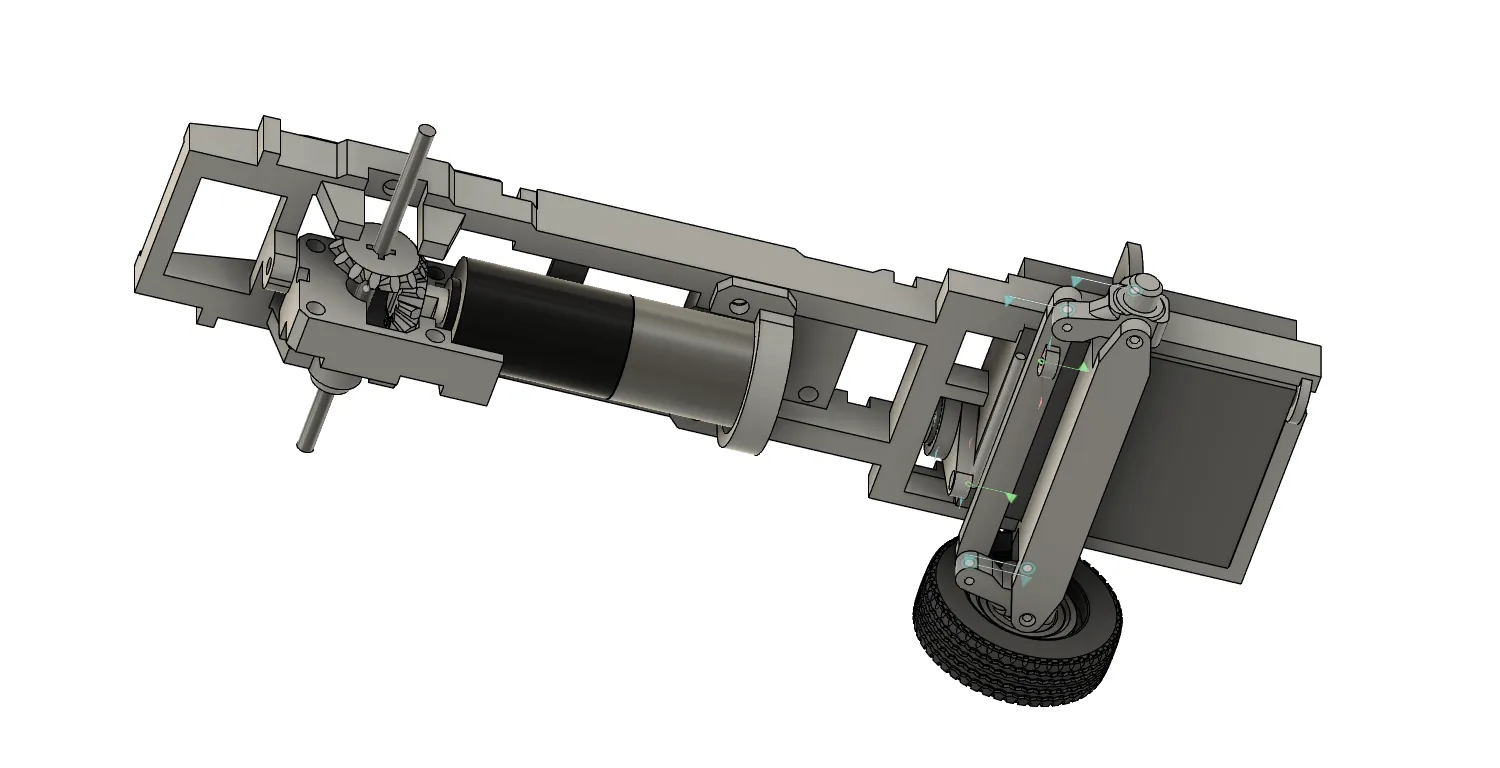
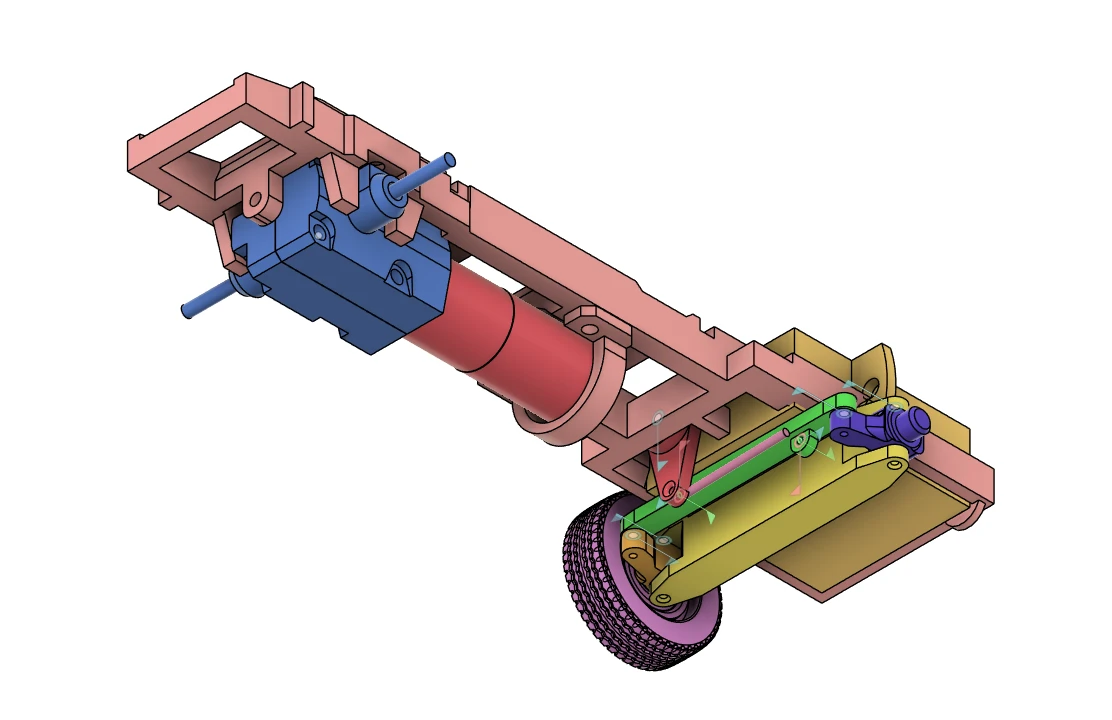
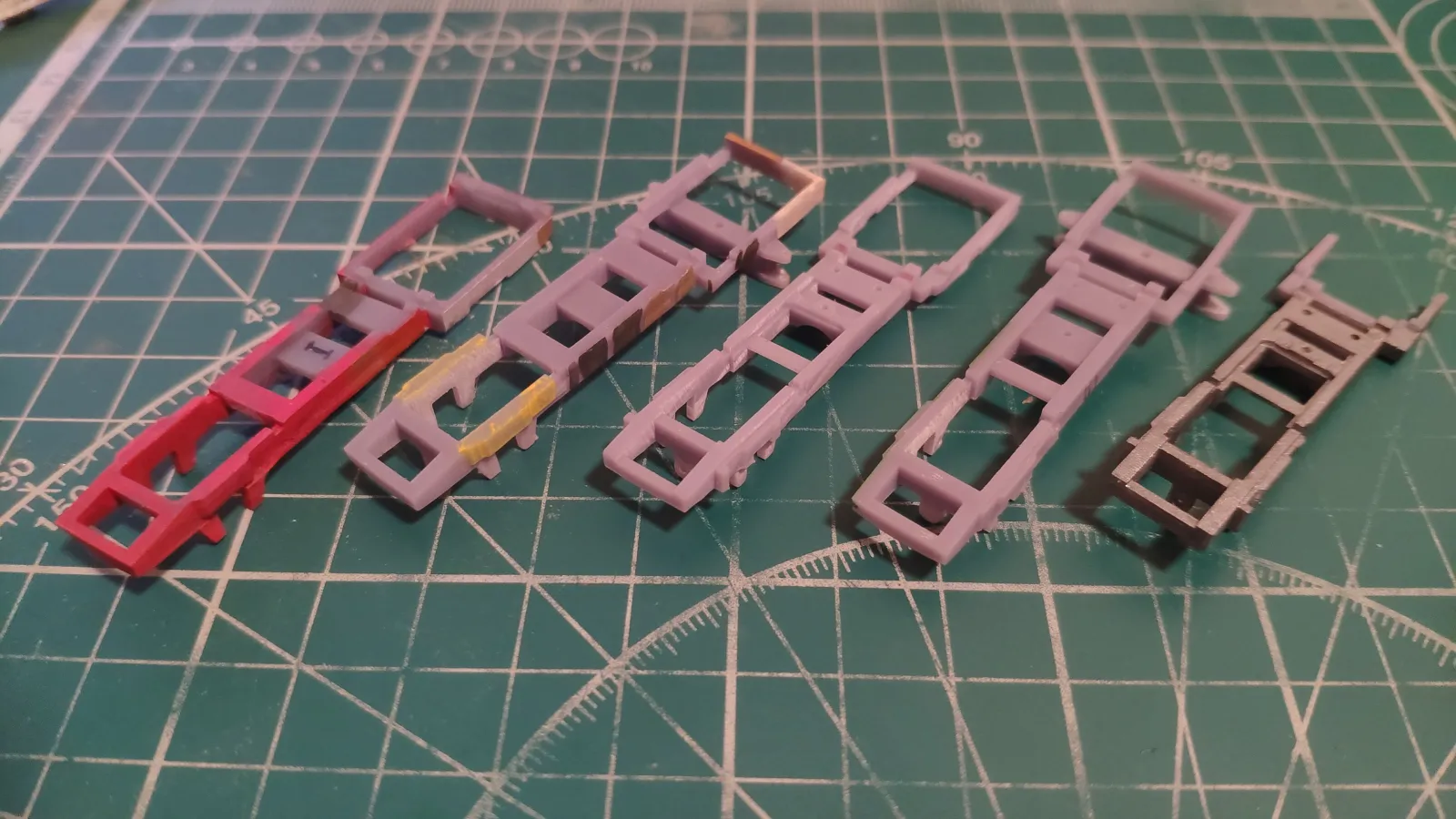
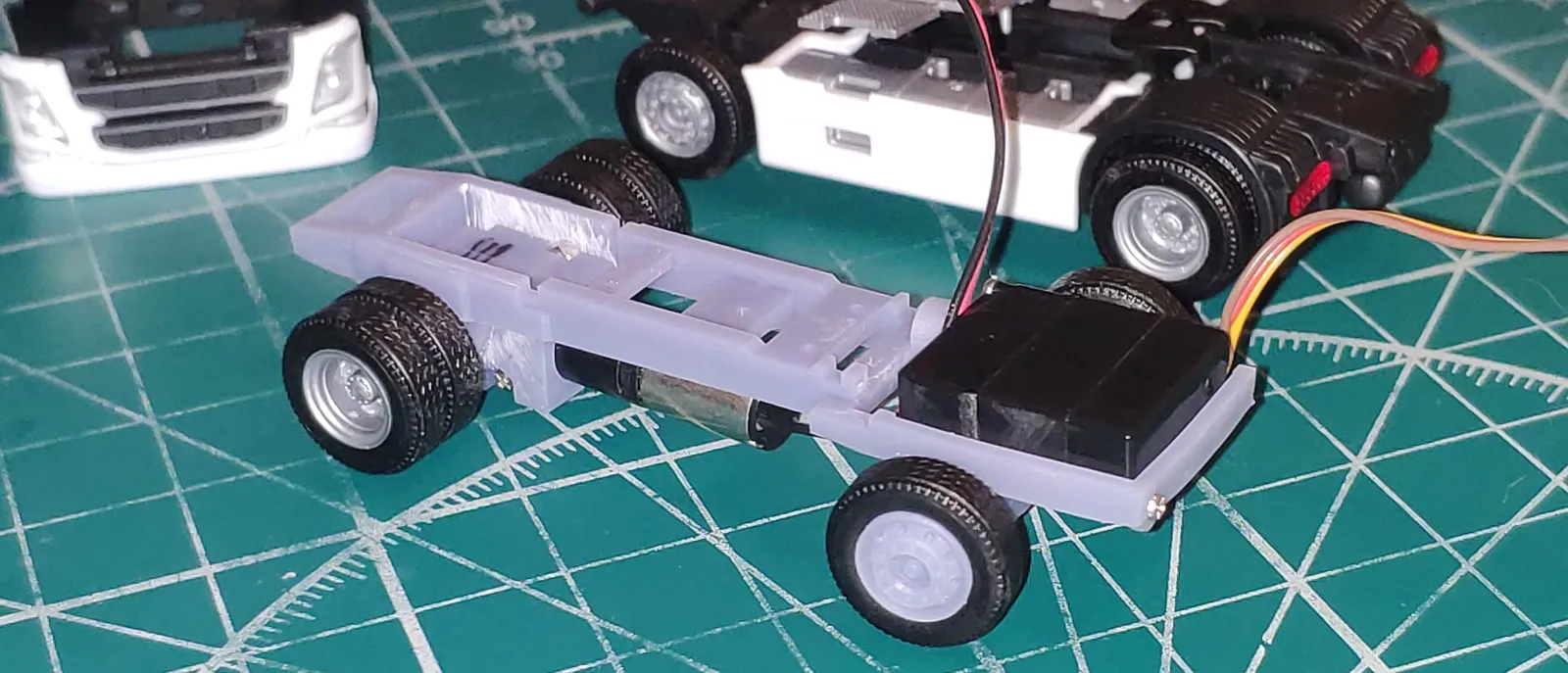
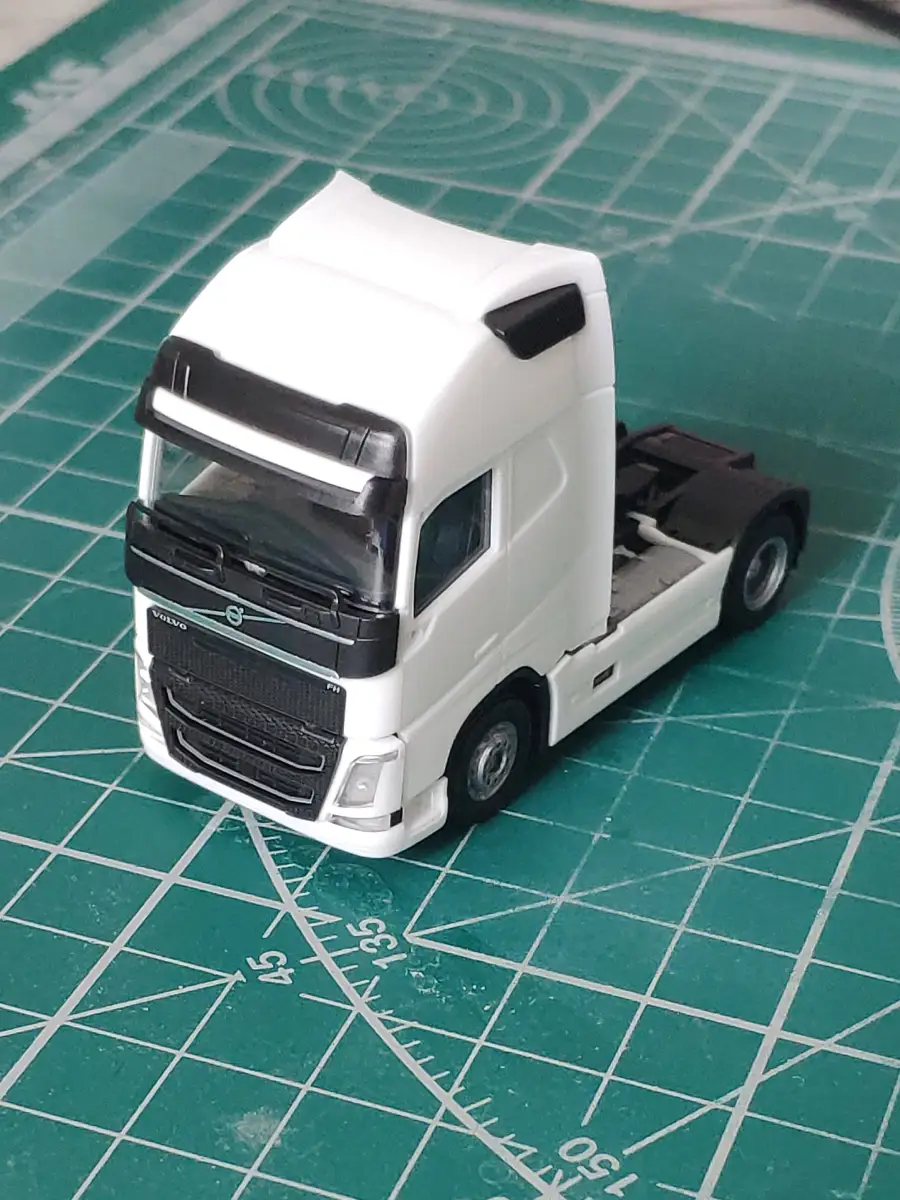
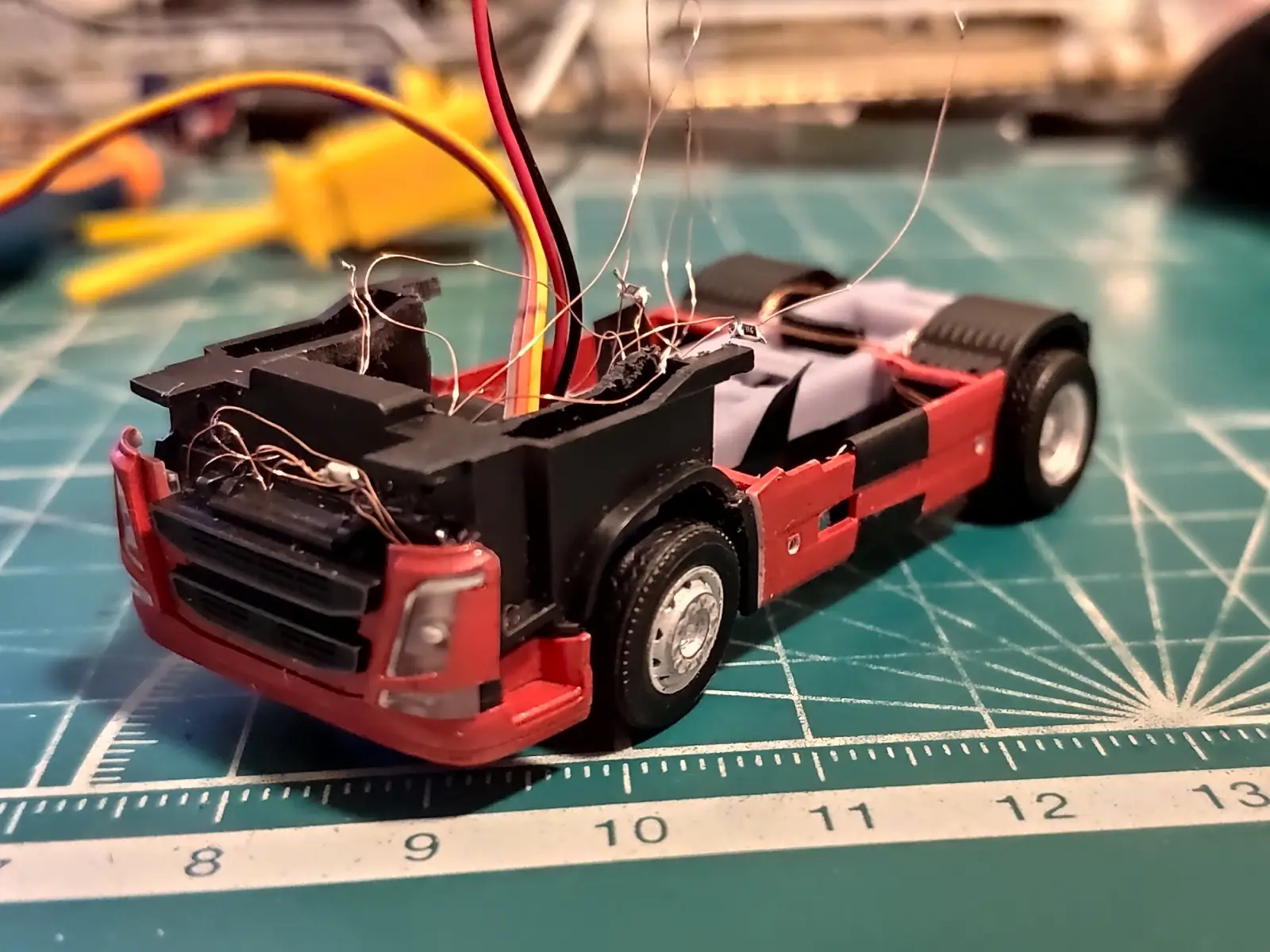
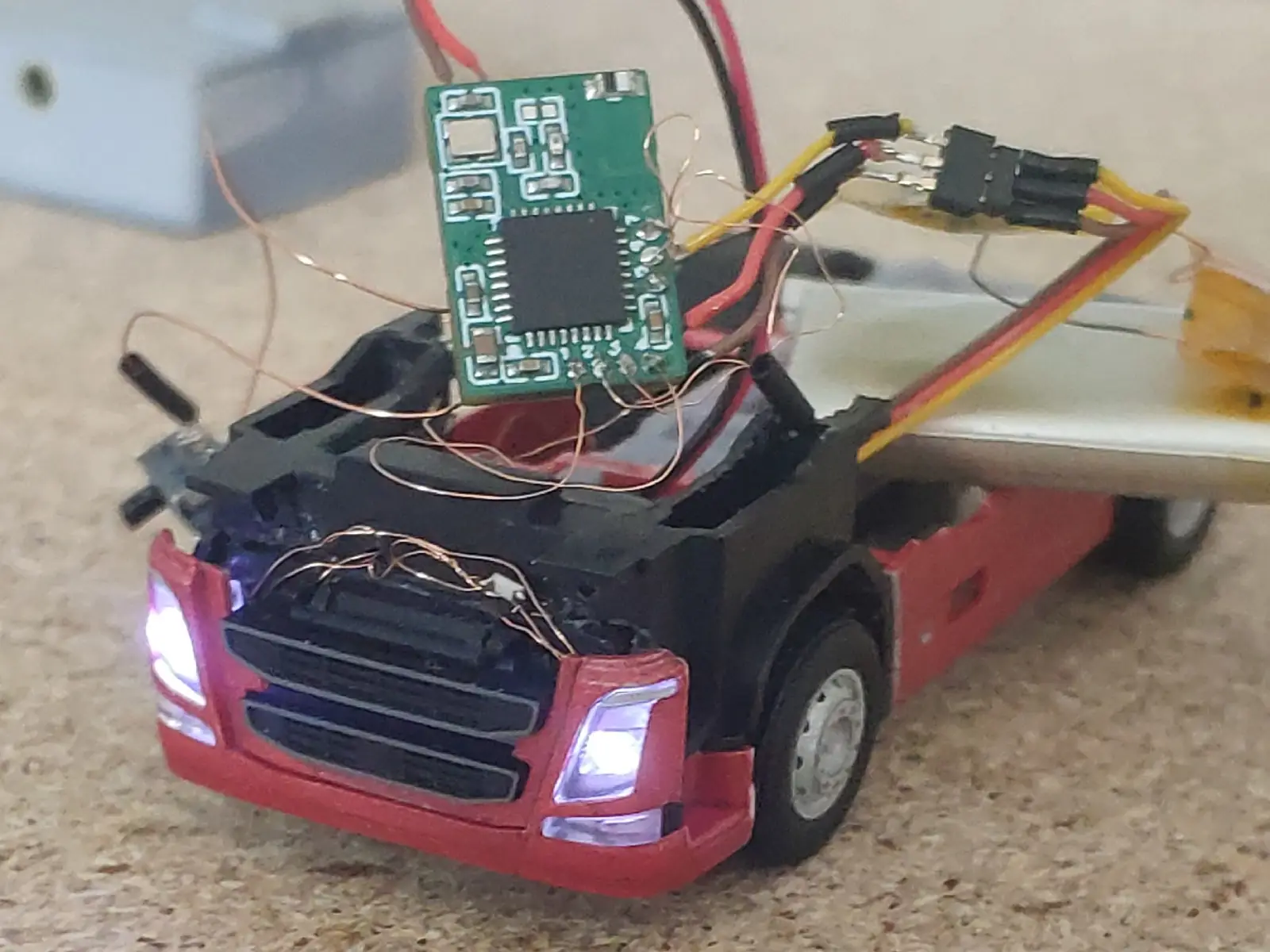
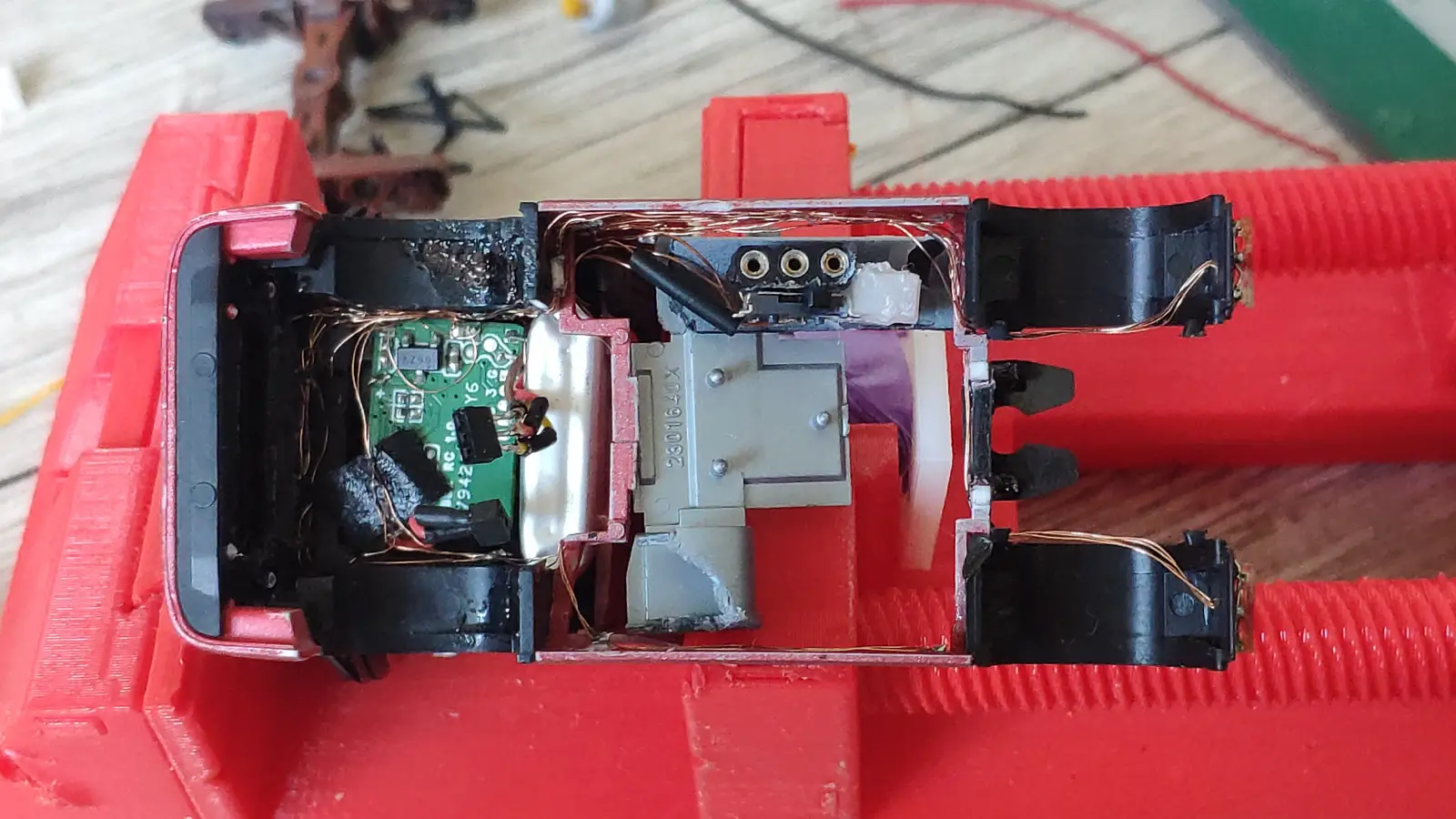
BOM
For the demo model, these components were bought (with sample aliexpress links where possible):
-
Herpa Volvo FH GL XL driver’s (084154) - for cabin
-
Herpa Volvo FH chassis for tractor (084178) - for skirts, tyres and rear axle and wheelhub
-
1.7g Servo (https://www.aliexpress.com/item/1005007086192907.html)
-
6mm gearmotor, 240RPM (https://www.aliexpress.com/item/1005004838212254.html)
-
Bearings, 682ZZ-1.5 2X5X1.5mm (https://www.aliexpress.com/item/33007670757.html)
-
Some M1 bolts and nuts (https://www.aliexpress.com/item/1005006023384565.html)
-
0.4mm copper wire
-
Optional: 1mm bushings (https://www.aliexpress.com/item/1005006010215331.html)
Drivetrain
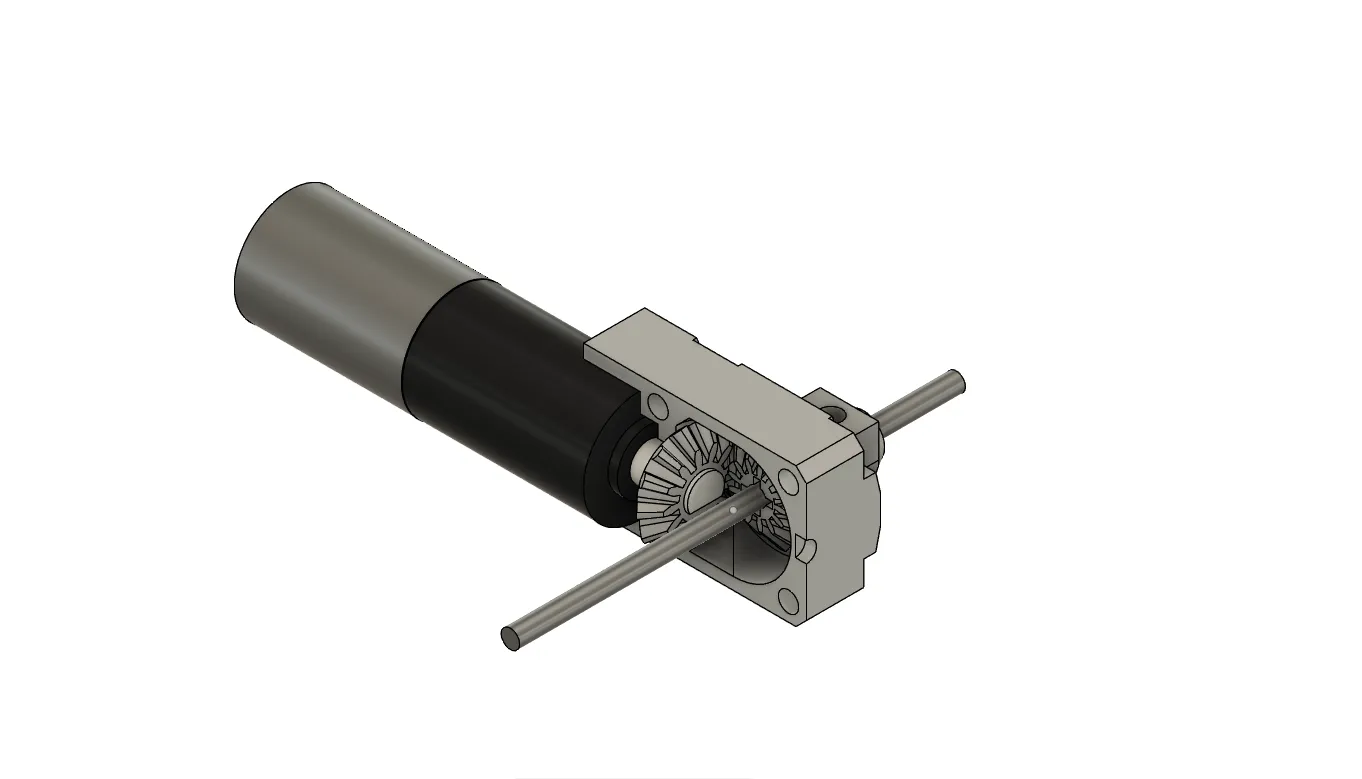
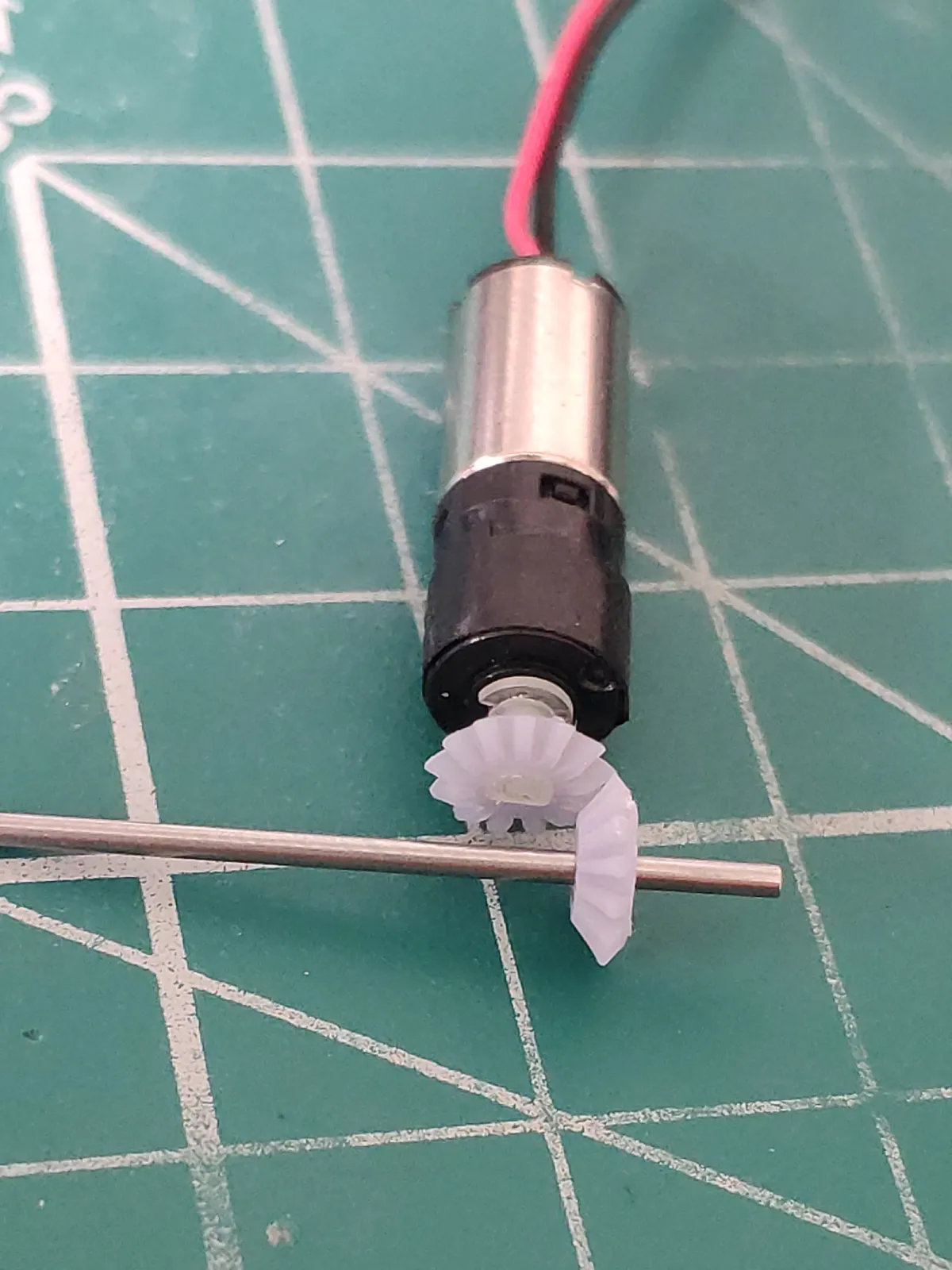
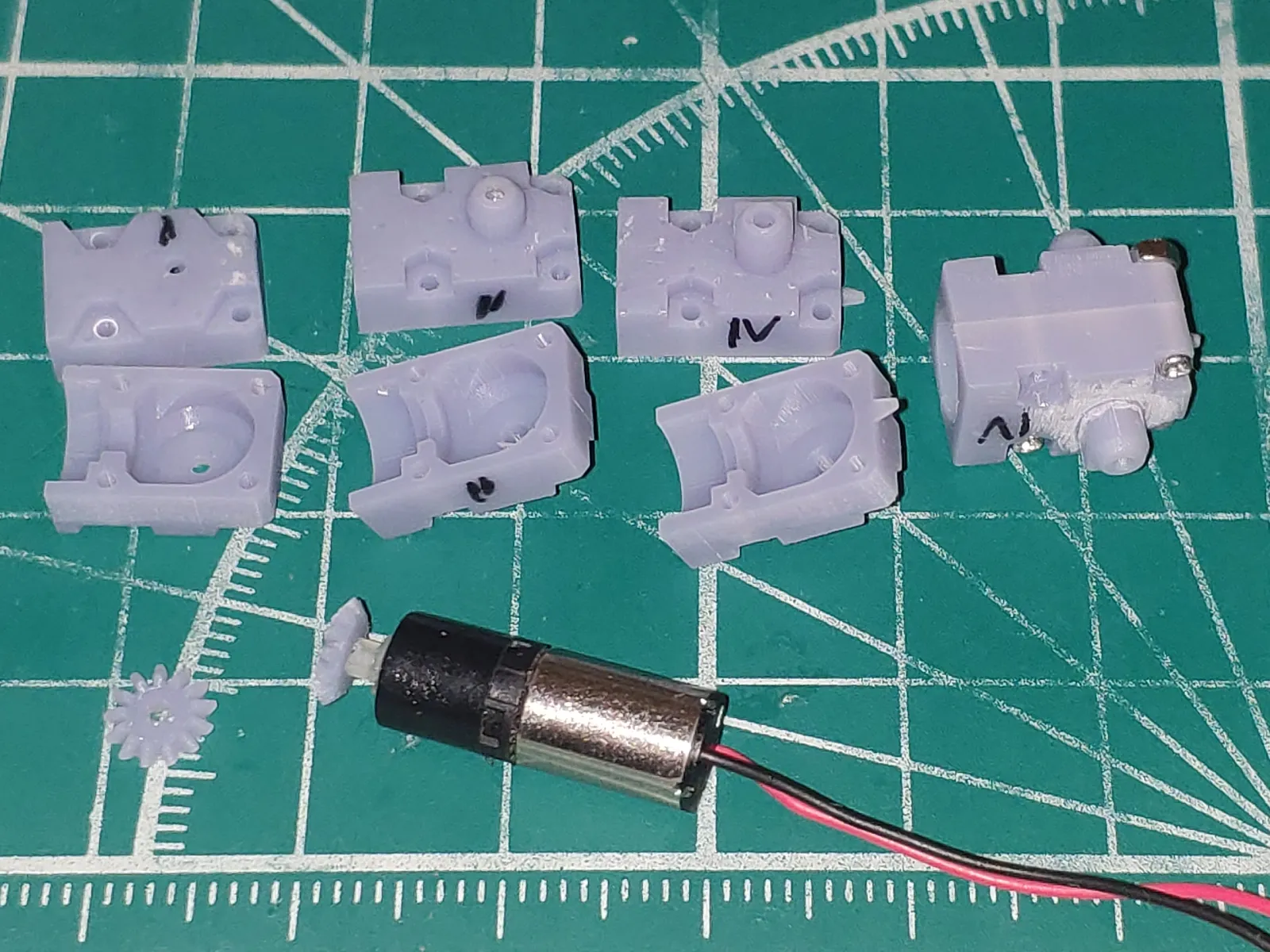
Materials
Currently I use Anycubic Standard resin that came with printer, and surprisingly the gears work fine. I lubricated them with silicone grease, and see no wear on them or on the housing. In future, I want to test Siraya Tech Fast Mecha White resin that has ceramic particles filler and is scratch-resistant.
Off-the-shelf parts
-
6mm DC gearmotor (AliExpress)
-
1mm steel axle
-
wheel hubs and tyres. I used ones from a Volvo FH16 truck from Herpa.
Steering
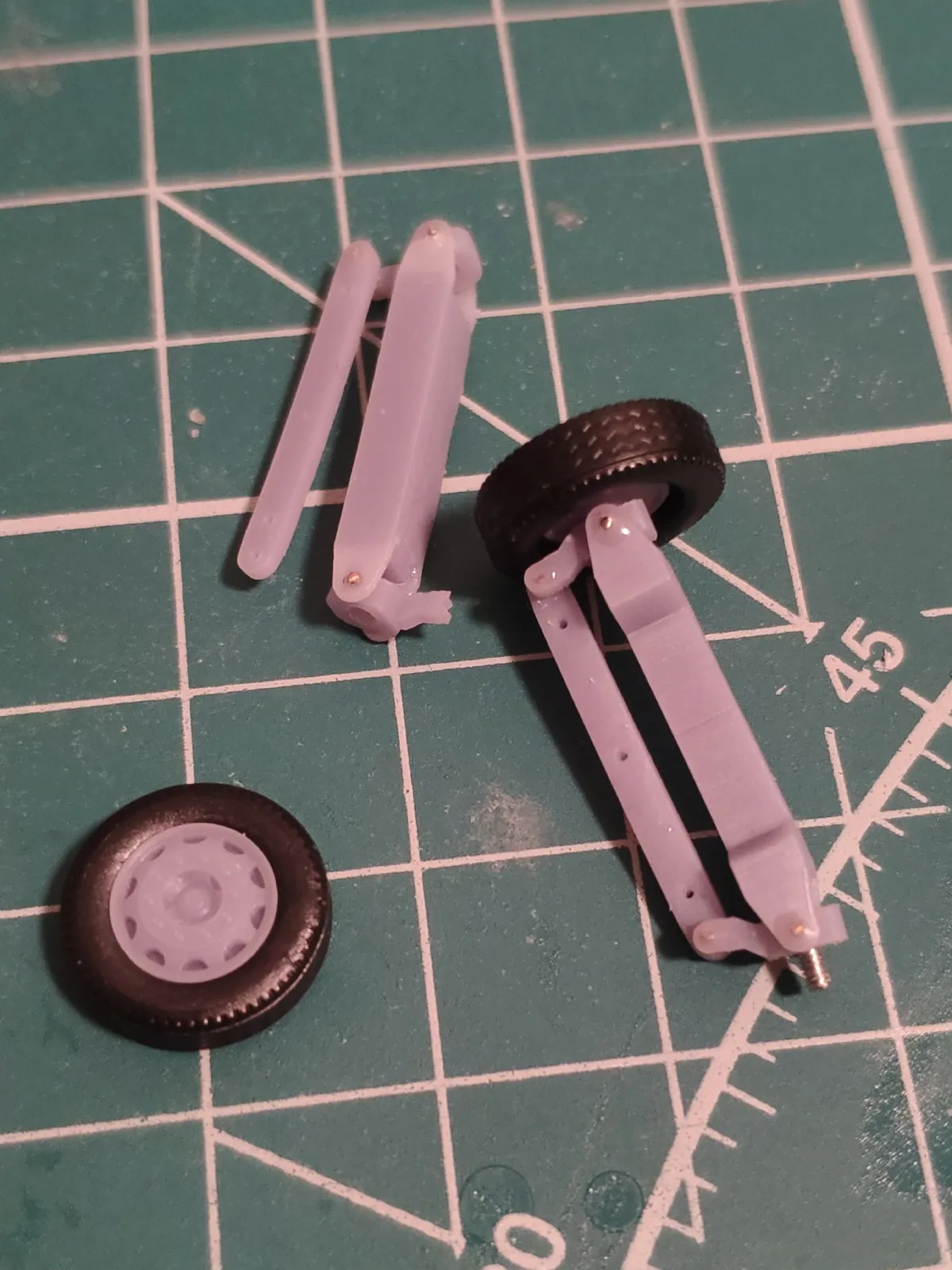
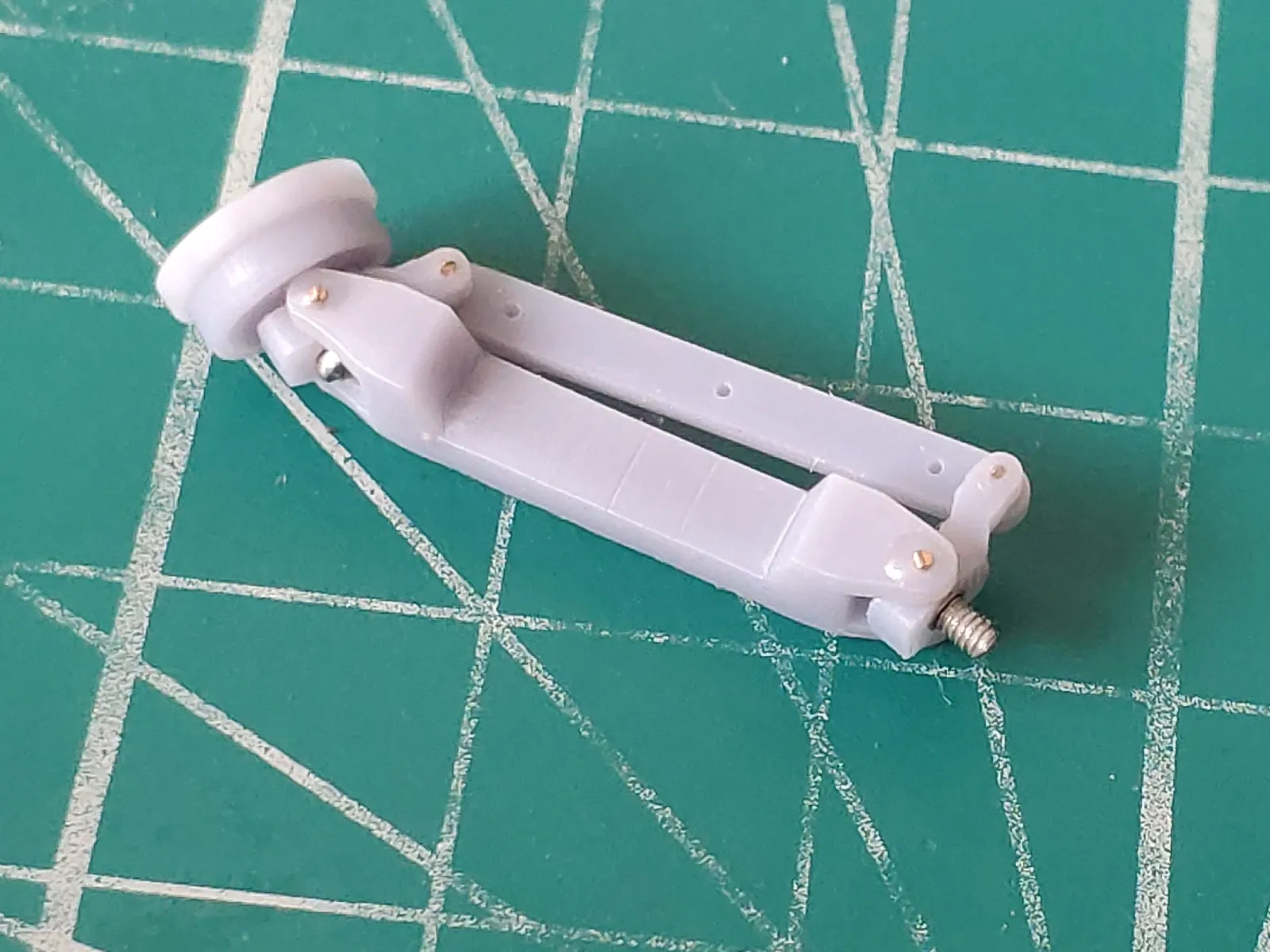
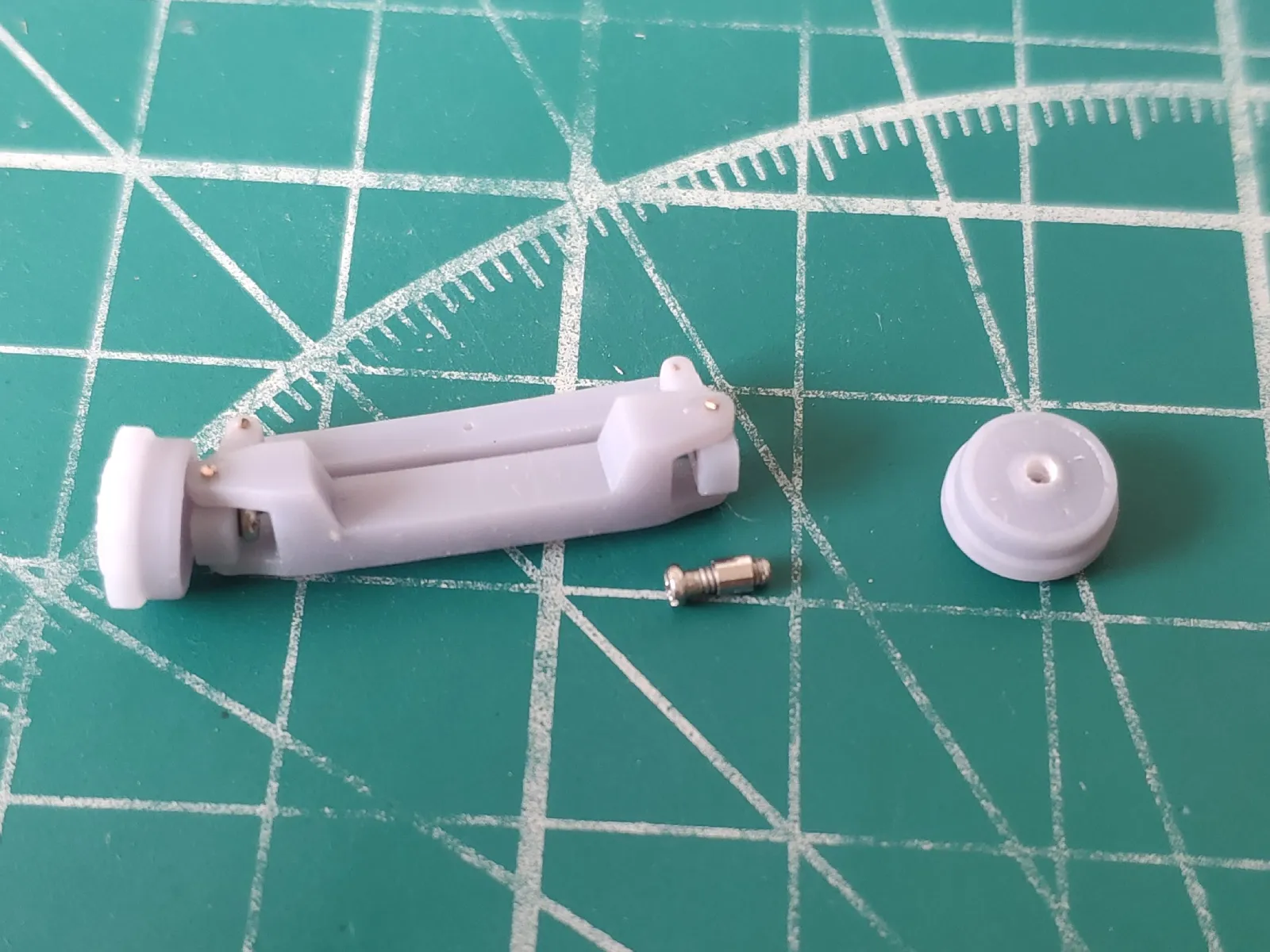

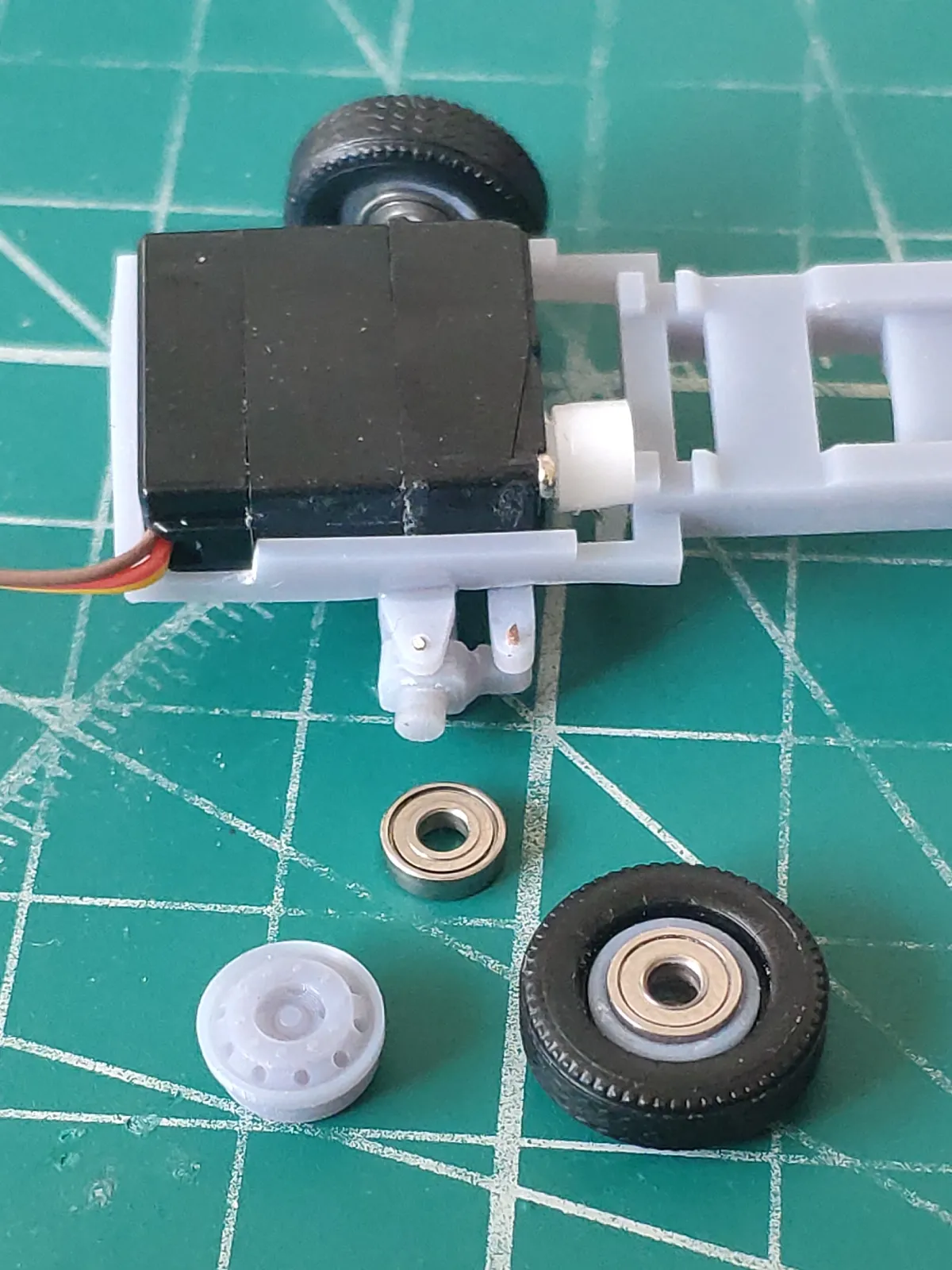
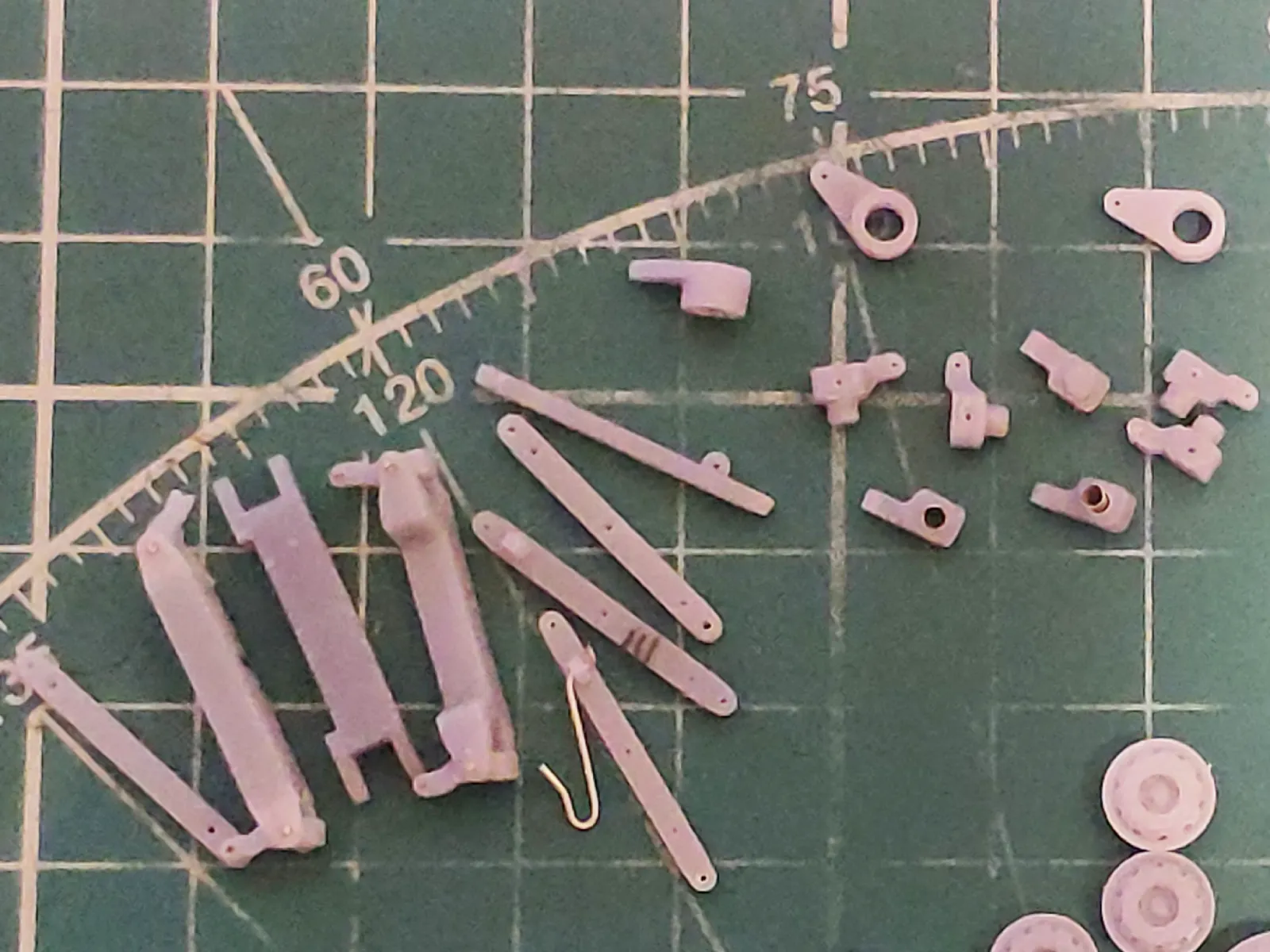
I’ve tried several approaches at connecting the wheel to steering knuckle.
First thing I’ve tried was M1 screw and a metal cable clamp (the one you secure steel cables with by pressing it around the cable). It was too wobbly as M1 screw is not precisely 1mm in diameter, and cable clamp is not precisely machined at all.
Second attempt was stacking 2 electric ferules inside one another. They come in various diameters, and some combinations can have a very tight fit, so they create a non-wobbly rotating connection. It had some axial wobble in my case though, as it was difficult to cut small pieces with flat perpendicular edge and without bending the walls.
It seems the above approach can be used, but in the end I used ball bearings inside the wheelhub, and plastic cylinder protruding from the steering knuckle, and it was just easier and quicker to assemble than ferules. So the latest version uses ball bearings (see photo above). One downside is that it is now impossible to put steering pivots inside the wheel, they bearings are too large.
Off-the-shelf parts
-
1.7g servo (AliExpress, $4)
-
Tyres. Again, I used ones from Herpa truck kit, but wheel hubs are 3D-printed.
-
A small amount or tough 0.4mm wire to connect all the rotating parts, I used phosphor bronze wire.
-
Piece of wire to connect servo arm with steering column, I used a through-hole resistor leg.
Tyres and wheelhub
I have made a 3D model of a truck tyre, but normal resin is too slippery and rigid to be usable as a rubber tyre. In future I want to try casting them in urethane rubber, but for now I use off-the-shelf Herpa tyres, they seem affordable enough and work well.
On the other hand, the front wheelhubs needed to be designed from scratch, as they don’t fit the steering mechanism. So I made a 3D model that was resin-printed. Several iterations of wheelhub details was made, as well as attachment system. After painting with chrome acrylic paints they look amazing.
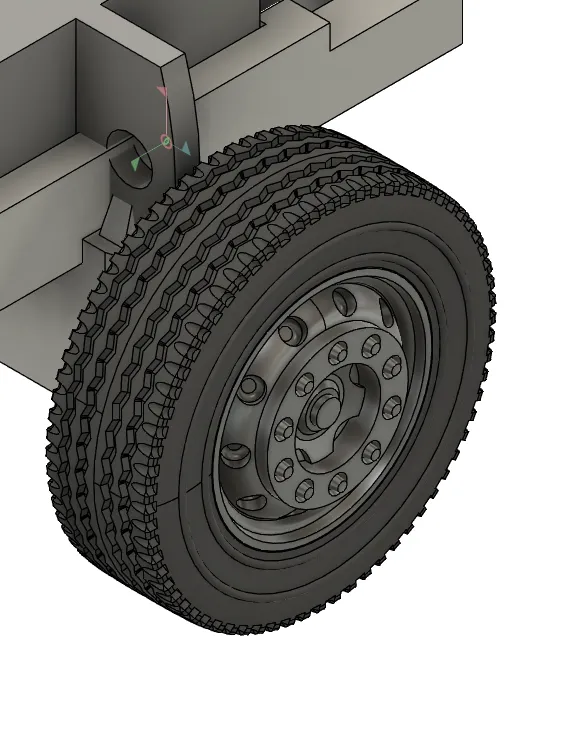

Electronics
The project uses a common RC servo and a DC motor, so usual ready-made RC receivers can be used (Deltang, Das87 etc). But as this is a DIY project, I’ve also designed a BLE RC receiver, it can be controlled from a smartphone and is open source.
The receiver project has its own page here.
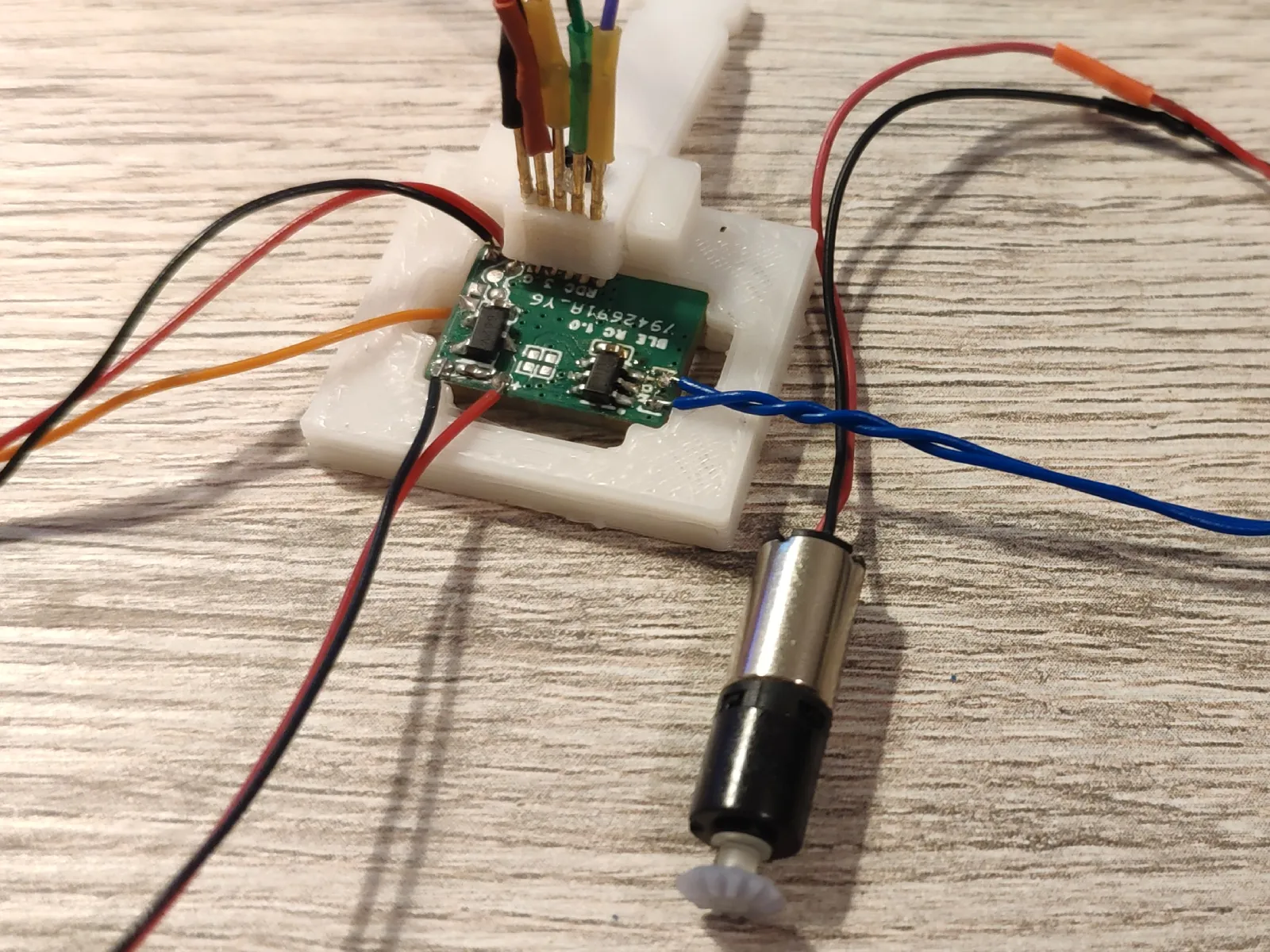